Materials chemistry: Chemical dealloying synthesizes new porous-carbon anode
04/26/2021
A process that can fabricate a bimodal porous carbon and tune each modal pore size independently
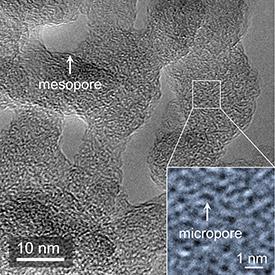
Adapted with permission from Ref. 1. Copyright (2021) American Chemical Society.
Researchers at AIMR have developed a sequential chemical dealloying technique for synthesizing 3D bimodal porous amorphous carbon with well-defined meso- and micropores1. With pore sizes and architecture tunable at the atomic scale, the amorphous-carbon product of this new, scalable process shows excellent performance as a sodium-ion battery anode.
Porous-material research strives to tailor pore architecture for interacting with the physical world, making it ideal for targeting transport phenomena, where cavity size, shape, and distribution control material properties.
To this end, a quintessential transport problem is the search for the next sodium-ion-battery hard-carbon anode. Even though numerous studies have shown that graphitic features such as surfaces, interlayers, and micropores can ameliorate sodium diffusion and storage, the sheer variety of hard-carbon defects makes definitive mechanisms difficult to pinpoint, and meaningful improvements hard to conceive.
That is, unless the improvement strategy targets a higher-performing hard carbon, whose 3D porous features are directly tunable by the novel fabrication method from the start. In this way, a team led by Mingwei Chen of AIMR at Tohoku University pioneered the use of dealloying as an advanced material-processing method to engineer new porous-carbon structures down to the angstrom level.
“The main obstacles to exploiting dealloying for porous carbon synthesis are the strong chemical bonds and the high chemical stability of most carbide precursors,” says Jiuhui Han, the first author of the study. “We overcame these obstacles by using a special Ni3C precursor that is in a metastable phase at room temperature.”
Using a two-stage dealloying process, the AIMR team produced a bimodal porous amorphous carbon. The first stage removes Mn from a Ni30Mn70 alloy, replacing it with carbon through carburization. The second stage removes Ni from the resulting metastable Ni3C alloy, yielding an amorphous carbon with coexisting meso- and micropores.
One key advantage of this method is that individual steps of the process control specific pore sizes: while more thermal coarsening of the pre-carburized Ni enlarges the mesopores, lower carburization temperatures enlarge the micropores.
The team tested the performance of the new bimodal porous carbon as a sodium-ion battery anode. They found that not only does the product have rapid diffusivities, excellent rate capacities, and long cycling stability compared with known hard carbons, but its transport properties are affected by specific features that are process-controlled.
Future plans will utilize different metal-carbide precursors to expand the tailoring capabilities of this process. “Our DFT calculations of bond strength predict a broad range of metal carbides as potential precursors for preparing porous carbon by dealloying,” says Han. “We will explore these metal carbides in the future.”
(Author: Patrick Han)
References
- Han, J., Li, H., Lu, Z., Huang, G., Johnson, I., Watanabe, K. & Chen, M. 3D bimodal porous amorphous carbon with self-similar porosity by low-temperature sequential chemical dealloying. Chemistry of Materials 33, 1013–1021 (2021). | article
This research highlight has been approved by the authors of the original article and all information and data contained within has been provided by said authors.