Nanoporous materials: A universal synthesis
02/26/2018
A generic, green route offers an easy way to make an extensive range of useful holey materials with tunable pore sizes
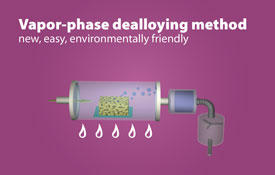
© 2018 Mingwei Chen
The first universal route to materials containing extensive networks of tiny voids has been developed by AIMR researchers1. It is a highly controlled, environmentally friendly approach to make so-called nanoporous materials, which are finding a growing number of applications thanks to their lightness, high internal surface areas, high electrical and thermal conductivities, and fast mass transport.
“Nanoporous materials are being used as large-surface functional materials for applications such as supercapacitors, electrodes for lithium ion and lithium–air batteries, and plasmonic materials for molecular detection,” explains Mingwei Chen, a lead researcher at the AIMR at Tohoku University and Johns Hopkins University, USA.
Typically, nanoporous materials are made using a process known as dealloying, which involves selectively removing one or more components from an alloy and leaving empty holes behind. But traditional electrochemical dealloying methods work on only a limited number of alloys and produce significant chemical waste.
In contrast, the novel vapor-phase dealloying approach developed by Chen’s team can in principle be used to make nanoporous versions of all stable solid elements in the periodic table. Furthermore, it produces no chemical waste and even captures the components removed from the alloys. “These recovered materials are highly pure and can be reused to make alloys or surface coatings,” says Chen.
His team built a bespoke dealloying system containing a high-temperature furnace, a vacuum system and a condensation trap for capturing vaporized alloy components (see image). Using the cobalt–zinc alloy Co5Zn21 as a model system, they explored the effects of varying the dealloying time, temperature and pressure on the size and location of the resulting pores. By tweaking these parameters, the researchers could tailor the size of cobalt’s pores from tens of nanometers to micrometers. For example, lower pressures in conjunction with slightly lower temperatures resulted in an even network of copious, very small pores. The evaporated zinc was fully recovered from the trap.
Chen has demonstrated this technique on eight zinc-containing alloys. “These materials span from inorganic to metallic elements, lightweight to noble metals, low-melting-point elements to refractory metals,” he says. The team is continuing to demonstrate the different nanoporous materials that can be made in this way.
“This is a scalable method for fabricating nanoporous materials,” Chen adds. His team can currently make tens of centimeters of material at a time, but it should be possible to scale it up for industry applications. But Chen first wants to better understand the process. “We have started the basic research to understand the kinetics of nanopore formation and evolution during vapor-phase dealloying.”
References
- Lu, Z., Li, C., Han, J., Zhang, F., Liu, P., Wang, H., Wang, Z., Cheng, C., Chen, L., Hirata, A. et al. Three-dimensional bicontinuous nanoporous materials by vapor phase dealloying. Nature Communications 9, 276 (2018). | article
This research highlight has been approved by the authors of the original article and all information and data contained within has been provided by said authors.