Sustainable chemistry: Made of greener stuff
07/25/2011
Fabricating catalysts into robust, nanoporous metallic glasses eliminates leaching problems during carbon coupling reactions
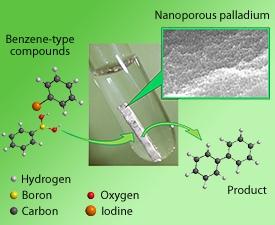
Convincing two organic molecules to connect through the formation of a carbon–carbon bond is never straightforward. The discovery that precious metals such as palladium can catalyze precisely such coupling reactions under mild conditions led to revolutionary advances in a range of fields, including the synthesis of pharmaceuticals and organic semiconductors. Unfortunately, palladium catalysts are toxic, expensive and difficult to separate completely from the final product. Handling issues can be circumvented through the use of a solid support, but gradual leaching of the metal into the surrounding solution can contaminate reactions.
Naoki Asao, Yoshinori Yamamoto and colleagues from the WPI-AIMR at Tohoku University1 have now developed a solid palladium-based ‘metallic glass’ that can repeatedly catalyze carbon coupling reactions with negligible leaching of the catalyst into the solvent. And thanks to an electrochemical fabrication technique that permeates the metallic glass with a uniform, nanoporous framework, the team’s recyclable catalyst shows excellent activity. Together, these two developments represent critical improvements for industries facing demands for safer, more sustainable chemical procedures.
Metallic glasses are stiff, strong alloys made by quickly cooling a mixture of atoms—in this case palladium, nickel and phosphorus—into an amorphous solid. The very dense packing of atoms in these materials affords them high resiliency, but the bulk metallic glasses are not catalytically active because only a small proportion of palladium atoms are sufficiently exposed to interact with organic reagents.
The team solved this problem by exploiting one of the ‘noble’ properties of palladium metals—a strong resistance to electrical corrosion. Asao explains that dipping a palladium–nickel–phosphorus metallic glass into an electrochemical etching solution dissolves the nickel and phosphorus atoms, while the palladium atoms agglomerate into a clustered, three-dimensional network. Due to the homogenous composition of the initial alloy, the resulting catalyst has a uniform distribution of pores of about 30 nanometers in diameter.
When the team performed a typical coupling reaction between two benzene rings bearing iodine and boron functional groups, they saw that the nanoporous catalyst gave the desired product in close to maximum yield (see figure). Even after reusing the catalyst four times, the coupling proceeded extremely efficiently. Further analyses also revealed that the amount of palladium lost into solution during the reaction was less than 0.0005% of the precious metal in each cycle.
“Contamination with palladium must be avoided, especially when the products are medicines,” says Yamamoto. “Our results demonstrate one way to solve the leaching problem, and give us hope that more innovations are possible, allowing nanoporous palladium to be developed as a robust ‘green’ catalyst.”
References
-
Tanaka, S., Kaneko, T., Asao, N., Yamamoto, Y., Chen, M., Zhang, W. & Inoue, A. A nanostructured skeleton catalyst: Suzuki-coupling with a reusable and sustainable nanoporous metallic glass Pd-catalyst. Chemical Communications 47, 5985–5987 (2011). | article
This research highlight has been approved by the authors of the original article and all information and data contained within has been provided by said authors.