Brief Review on Advanced Metallic Materials
Advanced Nonequilibrium
Materials,
including
Bulk Glassy Alloys
/ Bulk Metallic Glasses
Crystallization leading to
the formation of
:
Metallic Nanomaterials
Metallic Glassy –
(Quasi,Nano)Crystal Composites
Nanoquasicrystals
Partly based on the recently published book: Metallic Glasses and Their Composites
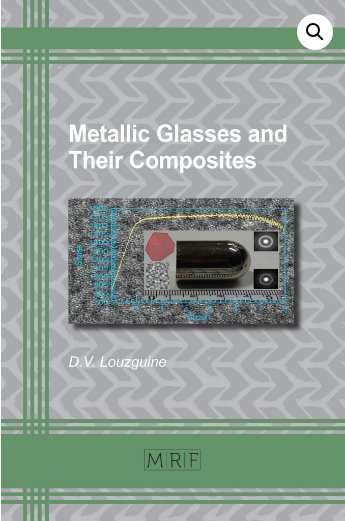
Active
research activities on metallic glassy alloys (or metallic
glasses) started after the formation of the first Au-Si sample with an
amorphous structure in 1960[1]
by rapid solidification. This become possible by using a rapid
solidification
technique for casting of metallic liquids at a very high solidification
rate of
106 K/s[2].
For a long time Pd-Cu-Si and Pd-Ni-P were known to be the best metallic
glass
formers[3]
. A large
number of
bulk glassy alloys (also called bulk metallic glasses) defined as
3-dimentional
massive glassy (amorphous) articles with a size of not less than 1 mm
in any
dimension have been produced during the last 30 years. These alloys
become
widely studied in 90-th. The high glass-forming ability achieved at
some
alloy compositions has enabled the production of bulk metallic glasses
in the
thickness range of 1-100 mm by using various casting processes[4],[5],[6].
Production of Glassy Alloys and Their General Features
Depending upon glass-forming ability
(GFA) glassy (amorphous) alloys can be
produced using various methods. Alloys having a low GFA can be prepared
in an
amorphous state (Fig. 1) by condensation from a vapor phase
[7]
,
[8]
.
This method is, however, highly power consuming and not efficient.
Various
alloys can be produced by a solid state reaction using mechanical
attrition
[9]
,
in
particular ball milling
[10]
or severe
plastic deformation
[11]
,
[12]
.
Electrodeposition from a solution is also possible
[13]
,
[14]
.
These methods are efficient but also power consuming.
|
Fig. 1. High-resolution TEM image of glassy
phase. The insert selected-area electron diffraction pattern. |
Much more productive is rapid
(compared to conventional metallurgical methods) solidification of a
liquid
phase[15],[16] by melt-spinning, Cu-mold casting,
liquid forging and so on. For example, Al-RE-TM (RE-rare earth metals, TM-transition metal) system glassy
alloys[17],[18]
were produced in a ribbon shape by the melt spinning technique[19]
or as powder using gas atomization technique[20]
as well as binary Al-RE alloys[21],[22].
An addition of Co partially replacing Y in the Al85Y10Ni5
(here and elsewhere alloy compositions are given in nominal atomic
percents
(at.%)) increased tensile fracture strength without worsening of bend
ductility[23].
Al85Y8Ni5Co2 alloy exhibits
one of
the largest supercooled liquid region on heating among the Al-based
metallic
glasses. A partial substitution of Y
by Mischmetal (Mm), a natural mixture of the RE elements, leads to a
drastic
decrease in the alloy cost without significant deterioration of the
mechanical
properties[24],[25].
Although
ease of devitrification of the Al-based glassy samples
connected with a high density of so-called quenched-in nuclei in some
glasses
as well as a low reduced glass-transition and devitrification
temperature in
the other glasses[26],
in general, impedes a limit on the sample’s critical thickness below 1
mm bulk
amorphous samples of high relative density were still obtained by warm
extrusion of atomized amorphous powder[27].
Bulk glassy alloys obtained
in the late 80-th (except for Pd-Cu-Si and Pd-Ni-P
obtained earlier2,3) with an extraordinary high GFA[28],[29],[30]
have larger size (comparable with conventional crystalline alloys)
of 1-100 mm. They can be obtained at the cooling rates of the
order of
100, 10, 1 K/s and even less[31],[32] much lower than 104-106 K/s required
for
vitrification of marginal glass-formers. The bulk glassy alloys possess
three
common features summarized by Inoue[33],
i.e., belong to multicomponent systems, have significant atomic size
ratios of
above 12% and exhibit negative heats of mixing among the constituent
elements. Cu-based bulk
glassy alloys wereobtained not only in the
ternary
Cu-(Zr or Hf)-Ti
[34]
but even in the binary Cu-(Zr or Hf)34,
[35]
,
[36]
,
[37]
systems. An
addition
of the third element like Ti or Al, for example,34 enhances
the
glass-forming ability of a binary alloy in accordance with the
“confusion”
principle which postulates that the multicomponent alloys in general
posses
better GFA than the binary alloys
[38]
.
Bulk glassy alloys exhibit high strength, hardness, wear resistance and large elastic deformation
(Fig. 2) and
high corrosion resistance , including passivation in some
solutions[39],[40].
Pt-based bulk metallic glass was reported to exhibit a
room-temperature strain of 20 % due to a high Poisson ratio of 0.42[41].
|
Fig. 2. Mechanical Properties of Bulk Glassy
Alloys in comparison with other materials. |
Bulk glassy alloys can be
thermo-mechanically shaped or welded in the supercooled liquid region.
Electromechanical shaping technology allows their rapid shaping by
Joule
heating at low applied stresses due to the high electrical resistivity
of
glassy alloys[42],[43].
Bonding of glassy alloys can also be achieved by friction welding[44].
Moreover, glassy alloys also exhibit superplasticity[45]
including
high-strain-rate superplasticity[46].
Glass-Forming Ability and General Properties
In
general bulk glassy alloys are formed at the compositions with
high Tg/Tl (Tg glass-transition
temperature, Tl
liquidus temperature) (Fig. 3) ratio exceeding approximately 0.6[47],[48].
At
the same time, it has been shown that the width of the
supercooled liquid region (dTx) (defined as Tx-Tg
where Tx is onset devitrification temperature) as indicator
of the
stability of the supercooled liquid against devitrification also
correlates
quite well with GFA . The
parameter gamma=Tx/(Tg+Tl) takes into account both criteria[49]
as high Tx and low Tg+Tl values
leading to
high gamma parameter
indicate rather low Tl and high dTx values.
The best glass-forming compositions
are not at the equilibrium eutectic point but somewhat shifted usually
towards
more refractory component
[50]
,
while Tg is not significantly different in the observed
range. This
is most likely due to the shift of the eutectic point with undercooling
at high
enough cooling rate as casting conditions of bulk glassy samples are
far from
the equilibrium conditions. This may be a result of deep undercooling
or
existence of the competing crystalline phases in the system. Both
factors may
cause a shift of the eutectic point.
However,
the principles for achieving a good GFA known so far are rather
indispensable
conditions which sometimes, however, are not sufficient[51].
The addition of Nd caused formation of an amorphous single phase only
in the
Ge-Ni-Nd alloy while no amorphous phase was formed in the Si-Ni-Nd
alloy. It
was found that the higher GFA of the Ge-Ni-Nd alloy compared to the
Si-Ni-Nd
one cannot be explained on the basis of the widely used parameters,
geometrical
and chemical factors, viscosity and diffusion data. It was suggested
that the
electronic structure characteristics, for example electronegativity
difference,
should be taken into consideration51.
It
has been shown that the electronegativity[52]
of the constituent elements is an important factor influencing glass
formation
and the temperature interval of the supercooled liquid region of the
glass-forming alloys[53],[54].
Packing
density for non-crystalline structures, as a geometrical
factor influencing GFA, has been verified using hard spheres model[55],[56].
A mixture of atoms with different sizes enables their more dense
packing than
can be achieved with separate phases. An importance of efficient atomic
packing
for the formation of metallic glasses was shown recently[57],[58].
It has been emphasized that specific radius ratios are preferred in the
compositions of metallic glasses. This features are also closely
connected with
so called l criterion
for good glass-forming ability[59],[60].
It
has been also supposed that electron concentration: number of valence
electrons
per number of atoms (e/a value) affect glass-forming ability[61],[62].
By
other words good glass-formers have definite electron concentration
values.
This rule has been proposed by analogy with Hume–Rothery phases related
to
certain valence electron concentration. However, as many glassy alloys
contain
transition metals which have multiple valencies, it is difficult to
decide
which valency value should be taken into consideration in a particular
case.
The
glass-transition
phenomenon in metallic glasses has been studied extensively. Three kinds of approaches have been formulated (see[63],[64], for example, among the other sources): (1) glassy phase is
just a frozen liquid, and thus, glass-transition is a kinetic
phenomenon and no
thermodynamic phase transformation takes place; (2) glass-transition
may be a
second-order transformation as follows from the shape of the curves for
the
thermodynamic parameters, for example, specific volume or enthalpy,
which
exhibit a continuity at the glass-transition temperature while their
derivatives like dV/dT or dCp/dT exhibit a discontinuity (in a
certain
approximation) at the glass-transition temperature; (3)
glass-transition may be
a first-order transformation as follows from the free-volume model.
Moreover, a thermodynamic aspect of
glass-transition has been pointed out by Kauzmann
[65]
.
A mode-coupling theory was also used to describe glass transition
[66]
.
Devitrification/Crystallization of Glassy Alloys Leading
to
Formation of a Nanostructure
Nanoscale
particles of a crystalline or a quasicrystalline phase can be readily
formed by
devitrification of the glassy alloys. This indirect method of
production of the
nanostructure requires formation of the glassy phase in the initial
stage and
its subsequent full or partial devitrification on heating. Such a
method leads
to the formation of a highly homogeneous dispersion of nanoparticles in
various
alloys. Nevertheless, a nanostructure can also be obtained directly
during
rapid solidification or casting at a certain cooling rate used.
However, in
such a case it is often difficult to adjust an appropriate cooling rate
and to
obtain a homogeneous structure.
Matrix phase prior to devitrification
can be amorphous, glassy or supercooled liquid. Although it might be
difficult
to establish an intrinsic physical difference between amorphous and
glassy
alloys such a slightly arbitrary differentiation is useful, especially
in
relation with devitrification behaviour. Here we define an alloy being
“amorphous” if it does not transform to a supercooled liquid before
devitrification (Fig. 3). In general glassy alloys exhibiting the
supercooled
liquid region on heating prior to devitrification have better
glass-forming
ability compared to amorphous alloys.
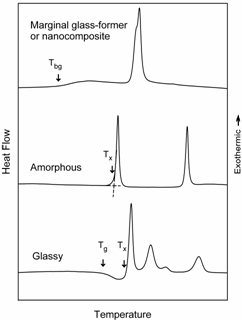 |
Fig. 3. Typical DSC traces representing glassy, amorphous
and marginal glass-forming alloy (or nanocomposite). |
Alloys devitrifying from the supercooled liquid exhibit a tendency to
form
metastable phases and phases with high crystallographic symmetry on
devitrification[67].
It may be connected with the change of the local atomic structure in
the
supercooled liquid region due to higher atomic mobility compared to
that in the
glassy phase. Below Tg
the crystalline products of devitrification inherit the as-solidified
structure
of the metallic glass.
Four
types of phase transformations were found to occur during
devitrification of
the glassy alloys: polymorphous (a product phase has the same
composition as
the glassy phase), primary (a product phase has a composition different
from
that of the glassy phase), eutectic devitrification (two or more phases
nucleate and grow conjointly) and spinodal decomposition involving a
phase
separation of the glassy phase prior to devitrification.
If
devitrification occurs by nucleation and growth mechanism
(amorphous alloy does not have pre-existing nuclei), then high
nucleation rate
leading to high number density of the precipitates of the order of more
than 1021
m-3 and low growth rate of the precipitating phase are
required in
order to obtain a nanostructure. The nucleation and growth processes
leading to
the formation of a nanostructure, including transient nucleation have
been
described in detail in several earlier works[68],[69].
The kinetics of the devitrification process has been also analyzed[70],[71].
Devitrification
of glassy alloys can be analyzed by Kolmogorov[72]
-Johnson-Mehl[73]
–Avrami[74]
-Kelton[75]
general exponential equation for the fraction transformed x(t):
|
(1) |
where I
and u are nucleation and growth rates,
respectively, while n is the Avrami exponent.
Nanostructured
alloys are readily obtained on primary
devitrification of glasses with a long-range diffusion controlled growth[76].
Another
type of phase transformation in an amorphous solid leading
to formation of a nanostructure is spinodal decomposition[77],[78].
For instance, it has been reported that in some Al–TM–RE glasses
devitrification leading to formation of a nanostructure appears to be
preceded
by the amorphous phase separation[79],[80].
Nevertheless, the most common mechanism
leading to formation of a nanostructure is primary devitrification.
Different Al-RE-TM glasses containing about 85 at.% Al show primary
precipitation of the Al solid solution (a-Al) nanoparticles on heating
[81]
,
[82]
with extremely high nucleation rate
exceeding 1020 m-3s-1
[83]
,
[84]
.
After
reaching a certain size a-Al particles change their morphology
from spherical to dendritic
[85]
.
Pressure effects on devitrification of the
Al-RE-TM alloys have also been studied
[86]
.
fcc a-Al lattice
parameter measurements and atom probe
ion field microscopy investigation[87]
showed
very low concentration of the alloying elements in nanocrystalline Al
in
accordance with the phase diagrams[88]
of Al-RE
and Al-TM. Segregation of the RE metal having low trace diffusivity in
Al on
the a-Al/amorphous phase interface
is
considered to be one of the most important reasons for the low growth
rate of a-Al. It is also important to note that
the primary devitrification requires a long-range diffusion that
impedes
crystal growth[89].
Clear
heterogeneous nucleation was observed during formation of the a-Fe nanocrystals[90],[91].
The structure of Fe-based soft magnetic alloys like: Finemet Fe73.5Cu1Nb3Si13.5B9[92]
and
Nanoperm Fe84Zr3.5Nb3.5B8Cu1[93]
after
annealing consists of bcc Fe nanocrystals below 20 nm in size finely
dispersed
in the amorphous matrix. Cu, Nb or Zr elements despite on their low
contents
are responsible for the formation of a nanostructure upon annealing.
For
example, devitrification of the Fe73.5Cu1Nb3Si13.5B9
alloy, which initially has an isotropic amorphous structure, starts
from the formation
of Cu-enriched zones[94].
As has been shown by means of atom
probe field ion microscopy as well as by high resolution transmission
electron
microscopy[95]
Cu forms nano clusters in the Fe73.5Si13.5B9Nb3Cu1
amorphous matrix which act as the sites for heterogeneous nucleation of
the bcc
Fe particles on devitrification[96].
The
density of the clusters estimated by three dimensional atom probe is in
the
order of 1024 m-3 at the average cluster size of
about
2-3 nm[97].
Not only pure metals and limited solid
solutions but intermetallic compounds can be formed with a nanoscale
size. For
example, the devitrification of
nanocrystal-forming
Ti-based alloys, for example, the Ti50Ni20Cu23Sn7
alloy begins from the primary precipitation of a nanoscale equiaxed,
almost
spherical particles of cF96 Ti2Ni solid solution phase
(other
alloying elements are partially dissolved in this phase) with a lattice
parameter of 1.138 nm[98],[99].
Formation of such a nanoscale cF96 phase having a large cubic unit cell
has
also been observed in the Zr- and Hf-based alloys[100],[101].
An
extremely small size and low growth rate of cF96 crystals were
observed in Hf55Co25Al20 glassy alloy.
This alloy undergoes a double-stage devitrification forming the primary
cubic
cF96 Hf2Co phase from the supercooled liquid by the steady state nucleation and
diffusion-controlled growth of nuclei followed by the subsequent
devitrification of the residual glassy matrix forming Hf2Al
and an unidentified phase. The cF96 nanoscale phase has a very low
average
growth rate of the order of 10-11 m/s. Very small cF96 Hf2Co
clusters of 2-5 nm in size are observed in a HRTM image of the annealed sample
(Fig. 4). Diffusional redistribution of Al within
the
glassy matrix may be the reason for the small growth rate of the
clusters. It
is interesting to note that although this alloy exhibits
devitrification by
nucleation and growth mechanism the local order of the cF96 clusters is
close
to that of the glassy phase[102].
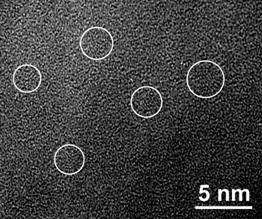 |
Fig. 4. High-resolution TEM image of the annealed Hf55Co25Al20
glassy alloy. |
In
many cases redistribution of the alloying elements on a short
scale precedes devitrification. For example, Mg-Ni-Mm and Mg-Ni-Y-Mm glassy alloys show a
multistage devitrification behaviour[103].
The amorphous Ge-Cr-Al-RE
alloys also exhibit local order changes prior to nanoscale
devitrification. For
example, some structure changes occur in the Ge70Cr16Al10Nd4
alloy prior to devitrification124. Primary Ge nanoparticles
are also
formed in many Ge-Al-Cr-RE alloys[104].
Anomalous X-ray scattering studied shows that Ge-Ge atomic pair in
Ge-Al-Cr
alloy has a different coordination compared to metal-metal and Ge-metal
pairs[105].
The
as-solidified microstructure of the rapidly solidified
Ge-Al-Cr-RE alloys examined by TEM showed the presence of finely
dispersed
zones homogeneously distributed in the amorphous matrix[106].
Their size is estimated to be about 1 nm[107].
These zones are responsible for the split of the first diffraction
maximum in
the SAED and XRD patterns. However, as the ordered zones are as small
as 1 nm
in size. An intermediate Ge-Ni-La compound which precipitates prior to
the
equilibrium phases in the Ge60Ni35La5
amorphous alloy may inherit the local atomic order of the amorphous
phase [108].
However, in many cases a
nano-dispersed
structure can be obtained directly from the melt upon rapid
solidification by
proper alloying. For example, the
microstructure of the
Si48Al20Fe10Ge7Ni5Cr5Zr5
alloy having an amorphous type X-ray diffraction pattern is
inhomogeneous and
contains Ge particles of less than 5 nm in size embedded in an
amorphous matrix
(Fig. 5)[109].
Ge having a lower mixing enthalpy with the other alloying elements than
Si is
rejected from the amorphous matrix and precipitates forming fine
nanoparticles,
though it has an unlimited solubility in Si.
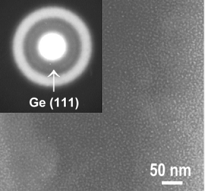 |
Fig. 5. dark-field electron micrograph of rapidly
solidified Si48Al20Fe10Ge7Ni5Cr5Zr5
alloy. The insert - selected-area electron diffraction pattern. |
Here
one should mention that the factors leading to
nano-devitrification of metallic glasses and amorphous alloys in many
cases are
not fully understood while several reasons are listed in the
literature. They
can be connected with the occurrence of heterogeneities such as oxygen
impurity-enriched clusters[110],
spinodal decomposition in the liquid or glass[111]
and homogeneous nucleation in partitioning systems[112].
The
time-temperature-transformation diagrams[113]
created in the isothermal mode or under continuos heating are useful
for
comparison of thermal stabilities of different glasses against
devitrification
as well as for the selection of the heat treatment regimes. Such
diagrams have
been created for different metallic glasses[114]
[115]
[116]
[117]
[118]
[119].
Comparison
of the long-term thermal stabilities of different
metallic glasses has been done using continuos heating transformation
CHT
diagrams[120].
CHT diagrams have been constructed by applying a corollary from the
Kissinger
analysis method using the DSC data at different heating rates.
CHT
diagrams also can be recalculated from the isothermal ones[121]
using a method close to that used for steels[122].
This method was proved to provide a good correspondence between the
data at
least in the mid-temperature range.
Not
only thermal activation but plastic deformation can cause nanoscale
devitrification of a glassy phase. For example, deformation
of some Al-RE-TM amorphous alloys at room temperature causes
precipitation of deformation-induced Al
particles of 7-10 nm in diameter within the shear bands on
bending[123]
or nano-indentation[124].
It has been suggested that a local temperature rise can play a role in
mechanically-induced devitrification[125].
However, further studies on nano-indentation of glassy alloys at low
strain
rates also showed the formation of the nanoparticles when local rise of
the
temperature due to adiabatic heating is not supposed to take place[126].
This postulate has been confirmed by bending test at low temperature
using dry
ice[127].
Nano-devitrification
leading to formation of quasicrystals
An icosahedral quasicrystalline
phase having a long-range quasiperiodic translational and an
icosahedral
orientational order, but with no three-dimensional translational
periodicity
was initially discovered in Al-Mn alloys[128] and later in the other binary Al-TM- based alloys containing Cr[129]
and V[130],[131]
and different ternary alloys[132].
The Al-TM base icosahedral structure has been presumed[133]
to consist of Mackay icosahedral clusters. Later the icosahedral phase was
observed
in
Ga-,
Ti-,
Mg- and Pd-based alloys ([134],
for example) as well as Cd-[135],
Rare Earth-[136]
and Zn-based[137]
alloys.
Quasicrystals can coexist with
rational approximant crystalline structures[138].
A
multiple twinning around an irrational axis of the approximants has
been
reported in an aggregate of fine size cubic crystallites[139].
A nanomaterial consisting of almost spherical
icosahedral particles with a diameter below 10 nm was obtained in Zr-Pt
alloy[140]
by
casting. An enhancement of the icosahedral short-range order in
the
supercooled Ti-Zr-Ni liquids decreases the barrier for the nucleation
of the
metastable icosahedral phase, even in the alloys in which the stable
crystalline phases are formed according to the equilibrium phase diagram[141],[142].
Reduced supercooling (undercooling)
before
crystallization from the melt was found to be the smallest for
quasicrystals,
larger for crystal approximants and the largest for crystal phases[143]. A low energy barrier for nucleation of
the icosahedral phase may explain the fact that only growth of the
pre-existed
icosahedral nuclei was observed in the Zr65Ni10Al7.5Cu7.5Ti10Ta10
alloy
[144]
.
Formation
of the nanoscale icosahedral phase was observed in the
devitrified Zr-Cu-Al, Zr-Al-Ni-Cu[145]
and Zr-Ti-Ni-Cu-Al[146]
glassy alloys containing an impurity of oxygen above about 1800 mass
ppm,
although no icosahedral phase is formed if oxygen content is lower than
1700
mass ppm. Recently, the nanoscale icosahedral phase was obtained in
devitrified
Zr-Al-Ni-Cu-Ag[147],
Zr-Al-Ni-Cu-Pd[148],
Zr-Ni-NM[149]
(NM-noble metals), Ti-Zr-Ni-Cu[150],
Zr-Al-Ni-Cu-(V, Nb or Ta)[151],
Zr-Pd[152]
and Zr-Pt[153],[154]
system alloys at much lower (typically about 800 mass ppm) oxygen
content. The
icosahedral phase is also formed in the Zr70Cu29Pd1
alloy at the very low Pd content[155].
It is
also noted that the icosahedral phase precipitates from the
supercooled liquid in Zr-based amorphous alloys containing the NM
elements. The
nanoscale icosahedral phase has been produced recently in the NM-free Zr-Cu-Ti-Ni[156]
and Zr-Al-Ni-Cu glassy alloys with low oxygen content below
500 mass ppm.
The
amorphous (glassy) ->
icosahedral
phase transformation, for example in a Zr65Al7.5Ni10Cu7.5Ag10
alloy, is not a polymorphous but rather a primary type reaction[157].
This explains the observed low growth rates.
The
local atomic structures around Pt as well as Zr in the amorphous
and quasicrystalline Zr70Al6Ni10Pt14
alloys have been determined by the anomalous X-ray scattering method[158].
Devitrification of several other Zr-based bulk metallic glasses has
been also
studied in situ using a high energy
monochromatic synchrotron beam diffraction in transmission on heating[159].
Transformation
from glassy+beta-Zr to
glassy+icosahedral structure was observed in Zr65Ni10Al7.5Cu7.5Ti5Nb5
alloy on heating by a
single-stage transformation with
diffusion control. b-Zr solid solution particles were found to dissolve in
the glassy phase while
the nanoscale particles of the icosahedral phase precipitate after the
completion
of the first exothermic reaction[160], which is considered to be a single-type
reaction in a certain sense
similar to peritectic one.
In the rapidly solidified TixZryHfzNi20
system alloys the nanoscale icosahedral phase is formed in the
composition
ranges close to the cI2 beta solid solution phase and complex cF96 phase formation ranges[161].
Moreover, cI2 b solid solution
and icosahedral phases were found to have close stochiometric
compositions.
This is not a surprising result as late-transition
metals (LTMs) have a high solubility in the cI2
b phase of
early-transition metals (ETMs).
The nanoscale
icosahedral quasicrystalline phase has been also produced upon heating
glassy
Hf65Pd17.5Ni10Al7.5[162],
Hf65Al7.5Ni10Cu12.5Pd5[163],
Hf59Ni8Cu20Al10Ti3[164]
and Hf65Au17.5(Ni,Cu)10Al7.5[165]
alloys (here and
elsewhere in the paper the (Ni,Cu)
symbol means Ni or Cu). Formation of the nanoscale icosahedral phase has
been also
found at an early devitrification stage of a binary Hf73Pd27
alloy[166].
According to the
quasilattice constant value, the icosahedral
phase in
the Hf65Pd17.5Ni10Al7.5, Hf65Au17.5Ni10Al7.5
and Hf65Au17.5Cu10Al7.5
alloys
consists of 137-atom Bergmann rhombic triacontahedra.
However, Hf-based alloys have a
higher tendency to form a cubic cF96 phase compared to Zr-based ones.
The
alloys in the systems in which an equilibrium Hf-based cF96 phase
exists do not
show the formation of the icosahedral phase from the amorphous matrix[167].
The
formation of the nanoscale icosahedral phase was recently
observed in the Cu-based alloys alloyed with Pd[168]
and Au[169]
while Ag- and Pt-bearing alloys did not form the icosahedral phase[170].
Replacing 5-10 at.% Cu
with Pd in the Cu60Zr30Ti10
glass-former
changes its devitrification pathway[171],[172],[173], inducing nucleation and
diffusion-controlled growth of a nanoicosahedral phase of about 3-10 nm
in size
(Fig. 6) consisting of rhombic triacontahedra from the supercooled
liquid region in the initial stage of the
devitrification process. A single initial devitrification reaction
takes place
in the Cu55Zr30Ti10Pd5
alloy while
in the Cu50Zr30Ti10Pd10
alloy a
combination of two reactions forming the icosahedral and crystalline
phase
takes place.
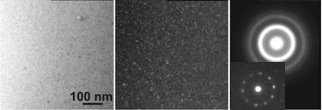 |
Fig. 6. TEM image of the annealed Cu55Zr30Ti10Pd5
alloy. (a)
Bright-field image, (b) dark-field image, (c) selected-area electron
diffraction pattern and (d) high-resolution image.
|
The
addition of 5 at.% Pd expands significantly the supercooled
liquid region in Cu-Zr-Ti alloy[174].
Cu-Zr-Ti[175]
alloy contains nanoscale crystalline particles (about 5 nm size) in
as-solidified state whereas the alloy containing 5 at.% Pd is amorphous174.
Nanoscale particles of the cP2
CuZr phase
were observed in the as-solidified Cu50Zr30Ti10Pd10
alloy. The dissolution of the CuZr
nanoparticles took
place on heating up to supercooled liquid region owing to the
instability of
the CuZr phase below 988 K[176].
According to the Cu-Zr
phase diagram, the CuZr phase undergoes eutectoid transformation at 988
K which
is above the supercooled liquid region of the Cu50Zr30Ti10Pd10
alloy (about 750-800 K). The nanoscale CuZr phase becomes
thermodynamically
unstable and dissolves in the supercooled liquid when atomic
diffusivity is
enhanced by temperature. One of the reasons is that the energy to form
an
eutectoid interface in nanoparticles is higher than the energy for
dissolution
of the nanocrystals.
High-Strength Nanocomposites Produced by
Devitrification
Devitrification of the
glassy alloys is the way of production of composite
nanomaterials. For
example, Zr65Al7.5Cu7.5Ni10Pd10
alloy having nanoscale icosahedral phase particles embedded in the
glassy
matrix shows better combination of the mechanical properties compared
to the
as-cast glassy sample
[177]
.
At the
same time, it is well known that stoichiometric icosahedral phase-based
alloys
have high hardness and are extremely brittle
[178]
.
It is
difficult to consider that the icosahedral phase itself in the present
alloys
has plastic deformability. The good mechanical properties are
attributed to the
existence of the residual intergranular glassy phase, though the volume
fraction of the glassy phase is estimated to be less than 5%. The
icosahedral
particles can act as a resistant medium against the shear deformation.
Nanocrystalline precipitates increase
the room temperature mechanical strength of the Zr-Al-Cu-Pd[179],
Zr-Al-Cu-Pd-Fe[180]
and (Zr/Ti)-Cu-Al-Ni[181]
bulk
alloys produced by crystallization of cast glassy samples. The
deformation behavior
of the partially crystallized Zr-based glassy alloys consisting of a
metallic
glassy matrix with crystallite precipitates of different shape and size
has
been studied recently[182].
Some
bulk glassy-crystal composites with enhanced ductility have been
produced by
proper alloying with the elements having zero or positive mixing
enthalpy with
main component, for example, in Zr-[183],[184]
and Cu-based alloys [185],[186].
Al-RE-TM
amorphous alloys posses a high tensile strength exceeding
1200 MPa[187]
and good bend ductility [188],[189]. The homogeneous dispersion of the nanoscale
fcc a-Al particles in
an amorphous matrix causes a drastic increase in
tensile fracture strength to 1560 MPa[190],[191]
. These
particles
can be formed by controlling the cooling rate upon solidification or by
annealing glassy alloys. An optimum
strength value was obtained when the
volume fraction of a-Al phase
reached 25%[192],[193].
The significant decrease in tensile fracture strength by the further
increase
in Vf is due to the embrittlement of the remaining amorphous
phase
by the progress of structural relaxation and the enrichment in the
solute
elements[194],[195].
However,
in some cases formation of the primary Al particles was found to deteriorate mechanical
properties. Partial substitution of Ni by Cu in
the
Al85Y8Ni5Co2 metallic glass
caused
formation of the nanoscale Al
particles. However, the tensile strength and hardness values
drastically
decreased[196]. Cu has much lower
absolute value of heat of mixing with Al, Y and Co than Ni[197] that leads to decrement of the
interatomic
constraint force. Thus, Cu may weaken the interaction needed for the
stability
of the glass, thus resulting in the disappearance of Tg and
precipitation of Al nanocrystals. In
addition, the volume fraction of the Al
nanocrystals
in Al85Y8Ni3Co2Cu2,
for
example, is much lower than that in the primarily devitrified Al85Y8Ni5Co2
metallic glass[198],[199].
Difference in devitrification pathways of
amorphous alloys depending on
heating rate, temperature and other conditions
Al85RE8Ni5Co2 glassy alloys showed precipitation of the a-Al nanoparticles after continuous
heating using DSC at high enough heating rates (0.67 K/s and higher) or
isothermal annealing at the temperature above Tg[200],[201]. At the same time, Y-,
Gd- and Dy-bearing metallic
glasses[202]
as well as the Al85Y4Nd4Ni5Co2[203] showed simultaneous formation of the
intermetallic compound(s) and a-Al nanoparticles, or primary formation of the
intermetallic compound
after annealing below Tg. For example, the Al85Y8Ni5Co2 alloy shows formation of an unknown
intermetallic compound conjointly with a-Al nanoparticles after isothermal annealing up
to the completion of the primary phase transformation below Tg
(Fig. 7). The
intermetallic
compounds are metastable and have a
multicomponent composition. The volume fraction of the intermetallic
compound
is higher than that of a-Al
and the fraction of a-Al
depends on annealing temperature below Tg.
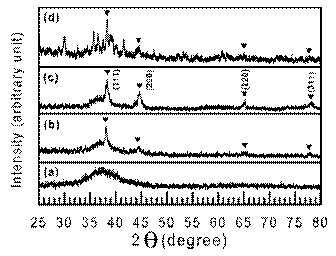 |
Fig. 7. XRD patterns, Al85Ni5Y4Nd4Co2
alloy. (a) - as-solidified, (b) - after DSC up to 571
K (above Tg), (c) - after DSC up to 638 K (above Tg),
(d) - after isothermal calorimetry at 543 K for 2000 s (below Tg).
DSC was scanned at 0.67 K/s. |
Two
crystalline phases: the equiaxed nanoscale Ge particles with the
size of about 3-20 nm and relatively large dendrites of a
multicomponent Ge18Cr4AlCeSm
crystalline phase of about 0.5 mm in size
precipitate simultaneously in the Ge68Cr14Al10Ce4Sm4
amorphous alloy on heating by a single-type exothermic reaction[204].
At the same time no eutectic-type coupled growth was observed. Ge and Ge18Cr4AlCeSm
phases in many cases have no common interface and are separated by the
amorphous
matrix. Moreover, the size and the volume fraction of the
multicomponent phase
depend on the heating rate whereas the size and distribution of the Ge
particles are independent of it. It can be suggested that Ge
nanoparticles grew
from the Ge–enriched zones formed during structural relaxation.
Nanocomposites produced
in-situ by rapid solidification.
The Al-Y-Ni-Co-Pd ribbon samples
have been produced by the melt-spinning technique. The addition of Pd
to
Al-Y-Ni-Co alloys caused disappearance of the supercooled liquid region
as well
as the formation of the highly dispersed primary a-Al nanoparticles about 3-7 nm in
size homogeneously embedded in the glassy matrix upon solidification
(Fig. 8).
An extremely high density of precipitates of the order of 1024
m-3
is obtained. The
resulted d-spacings of a-Al in Al85Y4Ni5Co2Pd4
correspond very well to that of FCC Al.
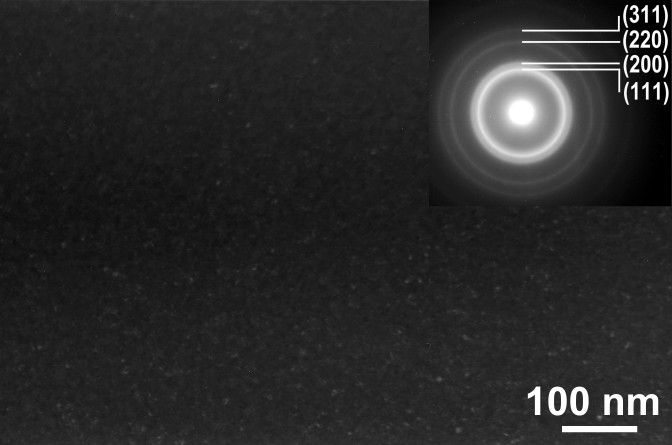 |
Fig. 8. The structure of the Al85Y4Ni5Co2Pd4
glassy alloy in as-solidified state, dark-field TEM image. The insert –
selected-area electron diffraction (SAED) pattern. Dark-field image (a)
was formed with the (200) diffraction ring of a-Al. |
The
first direct observation of micro-strain and dislocations
quenched in nanoparticles with a size below 7 nm was provided.
Summary
A
large number of metallic glassy alloys undergo
nano-devitrification on heating leading to the formation of nanoscale
crystalline or quasicrystalline particles. In some alloys this effect
leads to
the formation of the nanocomposites with enhanced mechanical properties
compared to fully glassy and fully crystalline alloys. Such alloys are
being
extensively studied at present and are believed to be important
structural
materials in the future.
References:
[1]. W. Clement, R. H. Willens and P. Duwez, Nature 187, 869
(1960)
[2]. H. S. Chen and D. Turnbull, J. Chem. Phys. 48, 2560
(1968)
[3]. H. S. Chen, Acta Metall. 22, 1505 (1974)
[4]. A. Inoue, Mater. Trans. JIM 36, 866 (1995)
[5]. W. L. Johnson, MRS Bull 24, 42 (1999)
[6]. A. Inoue, Acta Mater. 48, 279 (2000)
[7]. Nanomaterials: Synthesis, properties, and applications,
ed. A. S.
Edelstein, R. C. Cammarata, Bristol, Institute of Physics Publ. 596
(1996)
[8]. P. G. Le Comber, A. Madan and W. E. Spear, Electronic
and
Structural Properties of Amorphous Semiconductors. Ed. by P. G. Le
Comber and
J. Mort, Academic press, London
and New York,
373 (1973)
[9]. H. J. Fecht, Nanostructured Materials 6, 33 (1995)
[10]. A.W. Weeber and H. Bakker, Physica B153, 93 (1988)
[11]. R. Z. Valiev, Materials Science and Engineering A
234-236, 59
(1997)
[12]. V. M. Segal, Mater. Sci. Eng. A197, 157 (1995)
[13]. T. Yamasaki, P. Schlossmacher, K. Ehrlich and Y. Ogino,
Nanostructured Materials 10, 375 (1998)
[14] J. Ahmad, K. Asami, A. Takeuchi, D. V. Louzguine and A.
Inoue,
Materials Transactions, 44, 1942 (2003)
[15]. S. R. Elliot: Physics of Amorphous Materials, Longman
Group, Harlow, (1990)
[16]. B. Cantor, Materials Science Forum 307, 143 (1999)
[17]. A. Inoue, K. Ohtera, A. P.
Tsai and T. Masumoto, Jpn. J. Appl. Phys. 27, L280 (1988)
[18]. A. Inoue,
K. Ohtera and T. Masumoto, Jpn J Appl Phys
27, L1796 (1988)
[19]. Y. He, S. J. Poon, and G. J. Shiflet, Science 241, 1640
(1988)
[20]. A. Inoue and H.M. Kimura, Journal of Metastable and
Nanocrystalline Materials 9, 41 (2001)
[21]. A. Inoue, K. Ohtera, A. P.
Tsai, and T. Masumoto, Jpn. J. Appl. Phys. 27, L736 (1988)
[22]. A. Inoue, T. Zhang, K. Kita
and T. Masumoto, Mater. Trans. JIM 30, 870 (1989)
[23]. A. Inoue, N. Matsumoto and T.
Masumoto, Mater. Trans. JIM 31, 493 (1990)
[24]. D. V. Louzguine, and A. Inoue, J. Light Metals. 1, 105
(2001)
[25]. D. V. Louzguine, A. R. Yavari and A. Inoue, J.
Non-Cryst. Sol.
316, 255 (2003)
[26]. D. R. Allen, J. C. Foley and J. H. Perepezko, Acta
Mater. 46, 431
(1998)
[27]. A. Inoue and H.M. Kimura, J Light Met. 1, 31 (2001)
[28]. A. Inoue, A. Takeuchi, Materials Trans. 43, 1892 (2002)
[29]. W. H. Wang, C. Dong, C. H. Shek, Mater. Sci. Eng. R
44, 45
(2004)
[30]. J.F. Loffler, Intermetallics 11, 529 (2003)
[31]. T. Zhang, A. Inoue, and T. Masumoto, Mater. Trans., JIM
32, 1005
(1991)
[32]. A. Peker and W. L. Johnson, Appl. Phys. Lett. 63, 2342
(1993)
[33]. A. Inoue, Mater. Trans. JIM 36, 866 (1995)
[34]. A. Inoue, W. Zhang, T. Zhang
and K. Kurosaka, Acta Mater. 49, 2645 (2001)
[35]. D. Xu, B. Lohwongwatana, G. Duan, W. L. Johnson and C.
Garland,
Acta Mater. 52, 2621 (2004)
[36]. D. Wang, Y. Li, B. B. Sun, M. L. Sui, K. Lu, and E. Ma,
Appl.
Phys. Lett. 84, 4029 (2004)
[37]. A. Inoue, W. Zhang and J. Saida Mater. Trans. 45, 1153
(2004)
[38]. P. J. Desré, Materials Transactions, JIM 38, 583
(1997)
[39]. S. Pang, T. Zhang, K. Asami and A. Inoue, Materials
Science and
Engineering A, 375, 368 (2004)
[40]. W. H. Peter, R. A. Buchanan, C. T. Liu, P. K. Liaw, M.
L.
Morrison, J. A. Horton, C. A. Carmichael, Jr. and J. L. Wright
Intermetallics,
10, 1157 (2002)
[41]. J. Schroers and W. L. Johnson, Phys. Rev. Lett. 93,
255506 (2004)
[42]. M. de Oliveira, W. J. Botta F., A. R. Yavari, Materials
Transactions JIM 41, 1501 (2000)
[43]. A. R. Yavari, M. F. de Oliveira, C. S. Kiminami, A.
Inoue and W.
J. Botta, Mater. Sci. Eng.
A 375-377, 227 (2004)
[44]. T. Shoji, Y. Kawamura and Y. Ohno, Materials
Transactions 44, 1809
(2003)
[45]. Y. Kawamura, Т. Shibata, A. Inoue and T. Masumoto,
Scripta Mater.
37, 431 (1997).
[46]. M. Takagi, H. Iwata, T. Imura, Y. Soga, Y. Kawamura and
A. Inoue,
Materials Transactions, JIM 40, 804 (1999)
[47]. D. Turnbull and M. H. Cohen J. Chem. Phys. 34, 120
(1961)
[48]. A. Inoue and A. Takeuchi, Materials Transactions 43,
1892 (2002)
[49]. Z.P. Lu and C.T. Liu,
Acta Materialia 50, 3501 (2002)
[50]. H. Tan, Y. Zhang, D. Ma, Y.P. Feng and Y.
Li, Acta Materialia 51, 4551 (2003)
[51]. D. V. Louzguine, L. V.
Louzguina and A. Inoue, Appl.
Phys. Lett.
80, 1556 (2002)
[52]. L. Pauling, in The
Nature of
the Chemical Bond, Cornell Univ., USA, 3rd ed., 1960 p. 81
[53]. D. V. Louzguine, A. Inoue, Appl. Phys. Lett. 79, 3410 (2001)
[54]. X.K. Xi, D.Q. Zhao, M.X. Pan and W.H. Wang,
Intermetallics, in
Press.
[55]. J. D. Bernal, Proc. R. Soc. A., 280, 299 (1964)
[56]. W. M. Visscher and M. Bolsterli, Nature 239, 504 (1972)
[57]. D. B. Miracle, W. S. Sanders, O. N. Senkov, Phil. Mag.
83, 2409
(2003)
[58] H. W. Sheng, W. K. Luo, F. M. Alamgir, J. M. Bai and E.
Ma. Nature
439, 419 (2006)
[59]. T. Egami and Y. Waseda, J. Non-Cryst. Sol. 64, 113
(1984)
[60]. S. Ueno, Y. Waseda, in: W. Lee, R.S. Carbonara (Eds.),
Proceedings
of the Rapidly Solidified Materials Conference, 1986, p. 153.
[61]. C.H. Shek, Y.M. Wang and C. Dong, Materials Science and
Engineering A291 78 (2000)
[62]. Q. Jiang, B. Q. Chi, and J. C. Li, Appl. Phys. Lett.
82, 1247
(2003)
[63]. M. H. Cohen and G. S Grest,
Phys.
Rew. B 20, 1077 (1979)
[64]. A. Van Den Beukel and J. Sietsma, Acta Metall. Mater.
38, 383
(1990)
[65]. W. Kauzmann, Chem. Rev. 43, 219 (1948)
[66]. E. Leutheusser, Phys. Rev. A 29, 2765 (1984)
[67]. D. V. Louzguine and A. Inoue, Mater. Sci. and Eng. A
375-377,
346 (2004)
[68]. K. F. Kelton, Mater. Sci. Eng.
B32, 145
(1995)
[69]. J.H. Perepezko and
R.J. Hebert, J. Metall. 54, 34 (2002)
[70]. J. H. Perepezko, R. J. Hebert, W. S. Tong, Joe Hamann,
Harald R.
Rösner and Gerhard Wilde, Mater. Trans. 44, 1982 (2003)
[71]. J. H. Perepezko, R. J. Hebert and W. S. Tong,
Intermetallics 10,
1079 (2002)
[72]. A. N. Kolmogorov, Isz. Akad.
Nauk. USSR
Ser. Matem. 3, 355 (1937)
[73]. M. W. A. Johnson, and K. F.
Mehl, Trans. Am. Inst. Mining. Met. Eng. 135, 416 (1939)
[74]. M. Avrami, J. Chem. Phys. 9,
177 (1941)
[75]. K. F. Kelton, J. Non-Cryst.
Solids 163, 283 (1993)
[76]. A. R. Yavari and D. Negri, Nanostructured Materials 8,
969 (1997)
[77]. J. W. Cahn, Acta Metall. 9, 795 (1961)
[78]. S. Schneider, P. Thiyagarajan, U. Geyer and W. L.
Johnson, Physica
B: Condensed Matter, 241-243, 918 (1997)
[79]. A. K. Gangopadhyay, T. K. Croat and K. F. Kelton Acta
Mater. 48,
4035 (2000)
[80]. K. F. Kelton, T. K. Croat, A. K. Gangopadhyay, L. -Q.
Xing, A. L.
Greer, M. Weyland, X. Li and K. Rajan, J. Non-Cryst. Sol. 317, 71 (2003)
[81]. Y. H. Kim, A. Inoue and T.
Masumoto, Mater. Trans. JIM 32, 331 (1991)
[82]. M. Gogebakan, P. J. Warren and B. Cantor, Mater. Sci. Eng.,
A
226-228, 168 (1997)
[83]. J. C. Foley, D. R. Allen and J. H. Perepezko, Scripta
Mater. 35,
655 (1996)
[84]. M. Calin, A. Rudiger and U. Koester, J. Metastable and
Nanocryst.
Mater., 8, 359 (2000)
[85]. M. C. Gao and G. J. Shiflet, Intermetallics 10, 1131
(2002)
[86]. Y. X. Zhuang, J. Z. Jiang, T. J. Zhou, H. Rasmussen, L.
Gerward,
M. Mezouar, W. Crichton, and A. Inoue, Appl. Phys. Lett. 77, 4133
(2000).
[87]. K. Hono, Y. Zhang, A. P. Tsai, A. Inoue and T. Sakurai,
Scripta
Mater. 32, 191 (1995)
[88]. T. B. Massalski, Binary Alloy Phase Diagrams, ASM
International, Materials Park,
Ohio
(1990)
[89]. A. R. Yavari and D. Negri,
Nanostr. Mater. 8, 969 (1997)
[90]. A. R. Yavari and O. Drbohlav Mater. Trans. JIM 36, 896
(1995)
[91]. A. Mitra, H.-Y. Kim, D.V. Louzguine, N. Nishiyama, B.
Shen, A.
Inoue, Journal of Magnetism and Magnetic Materials 278, 299 (2004)
[92]. H. Yoshizawa, K. Yamauchi, T. Yamane and H. Sugihara,
J. Appl.
Phys. 64, 6047 (1988)
[93]. K. Suzuki, N. Kataoka, A.
Inoue, A. Makino and T Masumoto, Mater. Trans., JIM 31, 743 (1990)
[94]. K. Hono, Progress in Materials Science 47, 621 (2002)
[95]. K. Hono, K. Hiraga, Q. Wang, A. Inoue, T. Sakurai, Acta
Metall. et
Mater. 40, 2137 (1992)
[96]. W. J. Botta F., D. Negri, A. R. Yavari, J. Non-Cryst.
Sol. 247, 19
(1999)
[97]. M. Ohnuma, K. Hono, H. Onodera, J. S. Pedersen and S.
Linderoth,
Nanostructured Materials 12, 693 (1999)
[98]. D.
V. Louzguine and A. Inoue, Scripta
Materialia 43, 371 (2000)
[99]. G. He, J. Eckert and W. Loser, Acta Materialia 51, 1621
(2003)
[100]. Z. Altounian, E. Batalla, J.O. Strom-Olsen, J.L.
Walter, J. Appl
Phys 61, 149 (1987)
[101]. L. Q. Xing, J. Eckert, W.
Loser, L. Schultz and D. M. Herlach Phil. Mag. A 79, 1095 (1999)
[102]. D. V. Louzguine, H. Kato, H. S. Kim and A. Inoue, J.
Alloys and
Comp. 359, 198 (2003)
[103]. D. V. Louzguine, L. V. Louzguina and A. Inoue,
Philosophical
Magazine 83, 203 (2003)
[104]. D. V. Louzguine and
A. Inoue, Materials Letters 39, 211 (1999)
[105]. D. V. Louzguine, M. Saito, Y. Waseda and A. Inoue,
Journal of the
Physical Society of Japan,
68, 2298 (1999)
[106]. D. V. Louzguine and A.
Inoue, Mater. Trans., JIM 40, 485 (1999)
[107]. D. V. Louzguine and A.
Inoue, NanoStructured Materials 11, 115
(1999)
[108]. D. V. Louzguine, A. Takeuchi
and A. Inoue Journal of Non-Crystalline Solids 289, 196 (2001)
[109]. D. V. Louzguine and A. Inoue: Proc. 4-th Int. Conf.
IUMRS-ICA-97
(16-18 Sept. 1997, Mat. Res. Soc. Chiba, Tokyo),
the special issue of the Journal NanoStructured Materials, (1997), Vol.
8, p.
1007.
[110]. A. Inoue, Acta Mater. 48,
279 (2000)
[111]. S. Schneider, P.
Thiyagarajan, U. Geyer
and W. L. Johnson, Physica B 241-243, 918 (1998)
[112]. K. F. Kelton, Philos. Mag.
Lett. 77, 337
(1998)
[113]. J. W. Christian, The theory
of transformations in
Metals and
Alloys, Pergamon Press Ltd., Oxford, 1975, p. 369.
[114]. A. Peker and W. L. Johnson, Mater. Sci. Eng. A
179-180, 173 (1994)
[115]. N. Nishiyama and A. Inoue. Acta Mater. 47, 1487 (1999) .
[116]. J. Loeffler, J. Schroers and W.L. Johnson. Appl. Phys.
Lett. 77,
681 (2000) .
[117]. R. Janlewing and U. Köster, Mater. Sci. Eng.
A, 304-306, 833 (2001) .
[118]. J. H. Kim, S. G. Kim and A. Inoue. Acta Mater. 49, 615
(2001)
[119]. J. Schroers and W. L. Johnson, Mater. Sci. Eng. A
375-377,
781 (2004)
[120]. D. V. Louzguine and A. Inoue, Scripta Materialia 47,
887 (2002)
[121]. D. V. Louzguine-Luzgin and A. Inoue, Physica B:
Condensed Matter,
in press (2005)
[122]. R.A. Grange, J.M. Kiefer, Trans. ASM 29, 85 (1941)
[123]. H. Chen, Y. He, G. J. Shiflet, and S. J. Poon, Nature (London) 367, 541
(1994)
[124]. W. H. Jiang, F. E. Pinkerton, and M. Atzmon, J. Appl.
Phys. 93,
9287 (2003)
[125]. A. A. Csontos and G. J. Shiflet, Nanostruct. Mater. 9,
281 (1997)
[126]. J.-J. Kim, Y. Choi, S. Suresh, and A. S. Argon, Science
295, 654
(2002)
[127]. W. H. Jiang, F. E. Pinkerton, and M. Atzmon, Scr.
Mater. 48, 1195
(2003)
[128]. D. Shechtman, L. A. Blech, D. Gratias, J. W. Cahn,
Phys. Rev.
Lett. 53, 1951 (1984)
[129]. A. Inoue, H. M. Kimura, T. Masumoto, J. Mater. Sci. 22,
1758
(1987)
[130]. K. V. Rao, J. Fildler, H. S. Chen, Europhys. Lett. 1,
647 (1986)
[131]. A. Inoue, L. Arnberg, B. Lehtinen, M. Oguchi, T.
Msumoto, Metall.
Trans. 17A, 1657 (1986)
[132]. A. Inoue, H.M. Kimura, K. Kita, New Horizons in
Quasicrystals. ed.
by A. I. Goldman. D.J. Sordelet, P.A. Thiel and J.M. Dubois, World
Scientific, Singapore,
(1997)
[133]. Y. Elser and C.L. Henley, Phys. Rev. Lett. 55, 2883
(1985)
[134]. K.F. Kelton in Crystal Structures of Intermetallic
Compounds, J.
H. Westbrook and R. L. Fleischer Ed., John Wiley and Sons, New York,
(2000),
229
[135]. J.Q. Guo, E. Abe, A.P. Tsai, Jpn. J. Appl. Phys. 39,
L770 (2000)
[136]. M. J. Kramer, S. T. Hong, P. C. Canfield, I. R. Fisher,
J. D.
Corbett, Y. Zhu, A. I. Goldman, J. Alloys and Comp. 342, 82 (2002)
[137]. Y. Kaneko, Y. Arichika, T. Ishimasa, Phil. Mag. Lett.
81, 777
(2001)
[138]. K. F. Kelton, Materials Science and Engineering A
375-377, 31
(2004)
[139]. A. K. Srivastava and S.
Ranganathan,
Acta Materialia 44, 2935 (1996)
[140]. J. Saida, M. Matsushita and A. Inoue, Appl. Phys. Lett.
77, 1287
(2000)
[141]. K. F. Kelton, A. K. Gangopadhyay, G. W. Lee, L. Hannet,
R. W.
Hyers, S. Krishnan, M. B. Robinson, J. Rogers and T. J. Rathz Journal
of
Non-Crystalline Solids 312-314, 305 (2002)
[142]. K. F. Kelton, G.W. Lee, A. K. Gangopadhyay, R.W. Hyers,
T. J.
Rathz, J. R. Rogers,
M. B.
Robinson, and D. S. Robinson Phys. Rev. Lett. 90, 195504-1 (2003)
[143]. K.F. Kelton, J. Non-Cryst. Sol. 334-335, 253 (2004)
[144]. Lj. Ouyang, D. V. Louzguine, H. M. Kimura, T. Ohsuna,
S.
Ranganathan and A. Inoue, Journal of Metastable and Nanocrystalline
Materials
18, 37 (2003)
[145]. U. Koster, J. Meinhardt, S. Roos, and H. Liebertz,
Appl. Phys.
Lett. 69, 179 (1996)
[146]. L. Q. Xing, J. Eckert, W. Loser, and L. Schultz, Appl.
Phys. Lett.
73, 2110 (1998)
[147]. M. W. Chen, T. Zhang, A. Inoue, A. Sakai, and T.
Sakurai, Appl.
Phys. Lett. 75, 1697 (1999)
[148]. A. Inoue, T. Zhang, J. Saida, M. Matsushita, M.W. Chen,
and T.
Sakurai, Mater. Trans. JIM 40, 1137 (1999)
[149]. J. Saida, M. Matsushita, C.
Li, and A. Inoue, Appl. Phys. Lett. 76,
3558 (2000)
[150]. L. Wang, L. Ma and A. Inoue Mater. Trans. JIM 43, 2346
(2002)
[151]. J. Saida and A. Inoue, J. Non-Crys. Sol. 312-314, 502
(2002)
[152]. J. Saida, M. Matsushita, and A. Inoue, J. Appl. Phys.
88, 6081
(2000)
[153]. B. S. Murty, D. H. Ping, M. Ohnuma and K. Hono, Acta
Mater. 49,
3453 (2001)
[154]. J. Saida, M. Matsushita and A. Inoue, Journal of Alloys
and
Compounds 342, 18 (2002)
[155]. J. Saida, M. Matsushita and A. Inoue, Intermetallics
10, 1089
(2002)
[156]. D. V. Louzguine and A. Inoue,
Applied Physics Letters 78, 1841 (2001)
[157]. J. Z. Jiang, A. R. Rasmussen, C. H. Jensen ,Y. Lin, P.
L. Hansen,
Appl. Phys. Lett. 80, 2090 (2002)
[158]. E. Matsubara, M. Sakurai, T. Nakamura, M. Imafuku, S.
Sato, J.
Saida and A. Inoue, Scripta Materialia 44, 2297 (2001)
[159]. A. R. Yavari, A. Le Mouleca, A. Inoue, W. J. Botta F,
G. Vaughan
and A. Kvick, Materials Science and Engineering A 304-306, 34 (2001)
[160]. D. V. Louzguine, Lj. Ouyang, H. M. Kimura, A. Inoue,
Scripta
Mater. 50, 973 (2004)
[161]. N. Chen, D.V. Louzguine, S. Ranganathan, A. Inoue, Acta
Materialia
53, 759 (2005)
[162]. D. V. Louzguine, M. S. Ko, and
A. Inoue, Appl. Phys.
Lett. 76, 3424 (2000)
[163]. C. Li, J. Saida, M. Matsushita,
and A. Inoue, Appl. Phys. Lett. 77, 528 (2000)
[164]. C. Li, J. Saida, M. Matsushita, and A. Inoue, Philos.
Mag. Lett.
80, 621 (2000)
[165]. D. V. Louzguine, M. S. Ko, and
A. Inoue, Scripta Mater. 44,
637 (2001)
[166]. C. Li and A Inoue, Mater. Trans. JIM 42, 176 (2001)
[167]. D. V. Louzguine and A. Inoue Annales de Chimie - Science des Matériaux 27,
91 (2002)
[168]. D. V. Louzguine and A. Inoue, Scripta Materialia 48,
1325 (2003)
[169]. D. V. Louzguine and A. Inoue, J. Alloys and Compounds
361, 153
(2003)
[170]. D. V. Louzguine, H. Kato, A. Inoue, Science and
Technology of
Advanced Materials 4, 327 (2003)
[171]. D. V. Louzguine and A.
Inoue, J. Mater. Res. 17 (2002) 2112
[172]. J. Z. Jiang, B. Yang, K. Saksl, H. Franz, and N. Pryds,
J. Mater.
Res. 18, 895 (2003)
[173]. M. Kasai, J. Saida, M. Matsushita, T. Osuna, E.
Matsubara, and A
Inoue, Journal of Physics: Condensed Matter 14, 13867-77 (2002)
[174]. D. V. Louzguine, A. R. Yavari
and A. Inoue, Philosophical Magazine 83, 2989 (2003)
[175]. Y. Chen, T. Zhang, W. Zhan , D. Ping, K. Hono, A. Inoue
and T.
Sakurai, Materials Transactions. 43, 2647 (2002)
[176]. D. V. Louzguine, A. R. Yavari and A. Inoue, Appl. Phys.
Lett. 86,
041906-1 (2005)
[177]. A. Inoue, T. Zhang, M. W. Chen, T. Sakurai, J. Saida
and M.
Matsushita, Appl. Phys. Lett. 76, 967 (2000)
[178]. S. Takeuchi, Quasicrystals, Sangyotosho, Tokyo, (1992)
[179]. A. Inoue, C. Fan and A. Takeuchi, Journal of
Non-Crystalline
Solids 250-252, 724 (1999)
[180]. A. Inoue and C. Fan, Nanostructured Materials, 12, 741
(1999)
[181]. J. Eckert, U. Kühn, N. Mattern, A. Reger-Leonhard
and M. Heilmaier
Scripta Materialia, 44, 1587 (2001)
[182]. M. Heilmaier, Journal of Materials Processing
Technology 117, 374
(2001)
[183]. A. Inoue, C. Fan,
A. Takeuchi, Mater Sci Forum 307, 1 (1999)
[184]. T. C. Hufnagel, Cang Fan, R. T. Ott, J. Li and S.
Brennan, Intermetallics
10, 1163 (2002)
[185]. D. V. Louzguine, H. Kato, and A. Inoue, Appl. Phys.
Lett. 84, 1088
(2004)
[186]. C. Qin, W. Zhang, H. Kimura and A. Inoue, Mater. Trans.
45, 2936
(2004)
[187]. A. Inoue, K. Ohtera, A.P. Tsai and T. Masumoto, Jpn. J.
Appl.
Phys. 27, L280 (1988)
[188]. A. Inoue, K. Ohtera, A. P.
Tsai and T. Masumoto, Jpn. J. Appl. Phys. 27, L479 (1988)
[189]. G.J. Shiflet, Y. He and S.J.
Poon, J. Appl. Phys. 64, 6863 (1988)
[190]. Y.H. Kim, A. Inoue and T. Masumoto, Mater. Trans., JIM
31, 747 (1990)
[191]. Y. H. Kim, A. Inoue and T.
Masumoto, Mater. Trans. JIM 32, 599 (1991)
[192]. A. Inoue and H.M. Kimura, Mater. Sci. Forum 235-238,
873 (1997)
[193]. Y.-H. Kim, A. Inoue and T. Masumoto, Materials
Transactions JIM
32, 331 (1991)
[194]. A. Inoue, K. Nakazato, Y. Kawamura, A. P. Tsai and T.
Masumoto.
Materials Transactions, JIM 32, 331 (1991)
[195]. A. Inoue, K. Nakazato, Y. Kawamura, A.P. Tsai, T.
Msumoto. Mater.
Trans. JIM 35, 95 (1994)
[196]. D. V. Louzguine, A. Inoue, J. Mater. Res. 17, 1014
(2002)
[197]. A. Takeuchi and A. Inoue, Mater. Trans., JIM 41, 1372
(2000)
[198]. Y.H. Kim, A. Inoue, and T.
Masumoto, Mater. Trans. JIM 32, 599 (1991)
[199]. H. Chen, Y. He, G.J. Shiflet and S.J. Poon, Scripta
Mater. 25,
1421 (1991)
[200]. K. Pekala, P. Jaskiewicz, J.
Latuch and A. Kokoszkiewicz, J. Non-Cryst. Solids 211, 72 (1997)
[201]. N. Bassim, C. S. Kiminami and
M.J. Kaufman, J. Non-Cryst. Solids 273, 271 (2000)
[202]. D. V. Louzguine and A. Inoue, Journal of
Non-Crystalline Solids,
311, 281 (2002)
[203]. D. V. Louzguine and A. Inoue, Appl. Phys. Lett. 78, 3061
(2001)
[204]. D.
V. Louzguine, A. Takeuchi and A. Inoue, Journal of Materials Science 35, 5537 (2000)
Back to Main Menu |